At first glance, Bhujodi, a village located about 14 kilometres from Bhuj in Kutch district, appears quiet with nothing to set it apart. The village is built around a central road that branches off from the Bhuj-Anjar highway. Houses, largely one-storey structures, stand on both sides of the village road. On a sunny day, it is not uncommon to be greeted by warm drafts of wind outside. The traditional white, flat landscape of the district piercingly reflects the rays of the sun.
Things change at Vankar Vishram Valji’s residence. A rhythmic clickety-clack is heard periodically through the walls. Rows of dyed fabrics hang from ropes, strung across the courtyard, under the hot sun. Nearby, women wearing nose-pins and earrings and clad in resplendent outfits assiduously wind thread around bobbins. Their anklets pleasantly tinkle as they carry out their task.
Bhujodi is a major textile centre in Kutch district. There are 250 families in the village and all of them are weavers. Valji owns the largest number of looms and is the main employer in the hamlet. Close to 150 families from Bhujodi and the neighbouring villages work for him.
Weaving and Valji’s family go back several hundred years. He was felicitated as the Best Craftsman of the Year in 1974 by Prime Minister Indira Gandhi. Thanks to this recognition, tourists started making a beeline for Bhujodi.
Shamji, Valji’s son, along with his five brothers, have been overseeing the family business for more than two decades now. Visitors who arrive at Valji’s residence are taken around the in-house weaving unit. “Bhujodi receives approximately 15,000-30,000 tourists during the tourist season from November to February,” said Shamji.
Dressed in loose, white cotton clothes, Shamji meticulously displays several shawls, stoles, blankets, quilts, bed linen and bed covers. “Every piece is developed from scratch at our handloom facility.”
The process
The wool that is used to make most of the yarn is sourced from local cattle. Merino wool is imported from Australia for high-end products. “First we collect sheep wool and then we sort them according to [their] colours,” said Shamji. “The charkha is spun to generate the yarn from the fibre. Once the yarn is ready, we dye it in colours of our choice. Weaving the dyed fabric in a handloom to create the final article is the last stage of the production process. We use the extra-weft technique of weaving.”
All the products are handwoven by Shamji’s staff. Women from the Rabari or local cattle-herding community manufacture the yarn while the men work on the handlooms.
A mix of synthetic and natural colours are used to dye the clothes. Indigo leaves sourced from Bengaluru and Hyderabad are used to obtain shades of blue, while yellow is made from pomegranate skin or petals of the Palash flower (Butea Monosperma). Onion skin is used to impart a greenish-yellow tinge. The leaves of the local babul (Gum Arabic) are used to make black, while its skin is used procure a brown colour.
“We like to use natural colours which we manufacture at our residences, but sometimes customers demand colours like blood red,” said Shamji. “It is not possible to create such colours by using natural elements, so we buy synthetic colours from the markets of Bhuj.”
A simple stole or shawl takes a week to manufacture, while more elaborate ones such as intricately-detailed shawls, sarees and carpets can take as long as six months.
The journey
Till a few decades ago, the Ahirs, or the local farming community, and the Rabaris were the only clientele for the Bhujodi weavers. The Rabaris preferred black and white undyed yarn fabric, while the Ahirs liked bright colours. The linen manufactured at the time was heavy: a large shawl weighed more than three kilograms unlike today’s shawls that weigh about a kilogram. These shawls were used daily as well as for formal occasions like weddings.
After the devastating earthquake that shook Bhuj in 2001, the central and state governments made efforts to uplift the status of crafts in the Kutch region. Some of the measures included arranging exhibitions and fairs for the weavers to participate in. This led to collaborations with prominent fashion labels and designers such as Jaypore, 11.11 and Anita Dongre. The customer base expanded to cities across India and participation in international exhibitions also attracted the overseas market. “We initiated producing lightweight merchandise to suit the taste, convenience and pockets of the mass market,” said Shamji. “Nowadays, we regularly take part in exhibitions to reach markets beyond Kutch. Our workers earn Rs 15,000 to Rs 20,000 per month on average.”
Foreigners now constitute the major part of the growing customer base. Shawls and stoles start retailing around Rs 500 but the price of high-end shawls can go upwards of Rs 25,000. The sarees cost anywhere between Rs 5,000 and Rs 20,000.
Facing challenges
“Nowadays, customers want new designs at very short notice,” said Shamji. “Some want us to deliver at the speed of the e-commerce sites. But being a small community and given how labour-intensive our products are, it is not possible to meet those demands. The motifs and patterns we weave on the fabric are passed on to us by our forefathers: evolution takes its own time, it can’t happen overnight. Also, the weather and season play big roles in determining how fast we can finish making our products. In the monsoon month, dyeing takes a lot more time than in other seasons.”
Despite the gruelling nature of their job, the weavers of Bhujodi have never compromised on quality. “Our art is everything for us, we can never grow tired of it,” said Shamji.
All photos by Tania Banerjee.
Buy an annual Scroll Membership to support independent journalism and get special benefits.
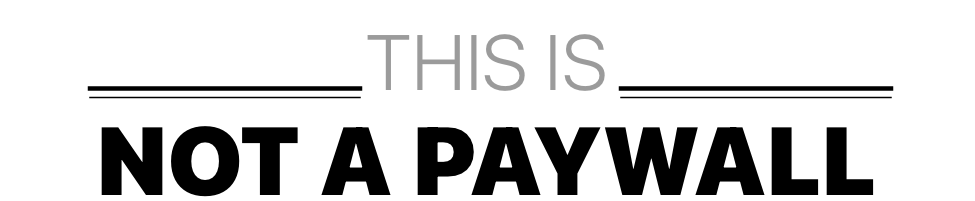
Our journalism is for everyone. But you can get special privileges by buying an annual Scroll Membership. Sign up today!