On Tuesday afternoon, the Baghjan oil field in Upper Assam’s Tinsukia district, operated by Oil India Limited, burst into flames. The blaze has claimed the lives of two firefighters so far. The loss of land, livelihoods, irreplaceable flora and fauna is yet to be measured in full.
The fire broke out exactly two weeks after a gas well in the area had started leaking gas and condensate uncontrollably. In other words, it was a blowout.
The company has not yet been able to ascertain what exactly sparked the blaze – there were clearing operations going on at the site when the fire broke out. But a blaze is almost inevitable after a blowout: with highly inflammable gas flowing uncontrollably in an area teeming with iron pipes and heavy machinery, all it requires is some friction.
To prevent a fire, Oil India Limited had been maintaining a “water umbrella” by continuously spraying water over the area. “We were lucky that it did not happen earlier,” said Oil India Limited’s spokesperson Tridiv Hazarika.
But luck ran out on the afternoon of June 9. So did the patience of people in the adjoining areas, many of whom had spent the last two weeks away from home in relief camps only to see their houses gutted on Tuesday. There have been protests that Oil India Limited claimed were “violent” and hampered their mitigation operations. The Assamese press has been critical, accusing Oil India, the country’s second-largest state-owned hydrocarbon exploration and production company, of being casual in its containment efforts. Reactions on social media have been scathing.
The censure has been two-pronged. First, that the blowout was a result of inadequate safety norms. Second, that efforts to contain the blowout have been too little, too late. The company has now said that it could take four more weeks to bring things under control.
Scroll.in spoke to several Oil India Limited officials and independent observers to piece together the events that led up to the blowout and the company’s response.
Most employees requested anonymity as the company has issued strict orders refraining anyone except the designated spokesperson from talking to the media.
A ‘workover’ operation
It began in the last week of May. A team set out to do a “workover” operation at well number five in the Baghjan oil field, on the fringes of the Dibru-Saikhowa National Park. In oil parlance, a workover is a complex, invasive operation to extend the life of a well.
Well number five had been a high performer in earlier times but its yield was starting to get erratic. This called for an intervention. A new sand zone at a different depth in the well had to be targeted for production. Oil India Limited had signed a contract with the Gujarat-based John Energy Limited to carry out the exercise.
First, as the standard protocol goes, the well was “killed”. Extraneous pressure exceeding the pressure at the old production zone was applied using a brine solution. The objective was to prevent gas from rising to the surface.
Then, the blowout preventer, a large valve that is mounted on top of the well to keep a tab on the pressure of the gas and to seal it, was installed.
Then began the actual workover operation. A cement barrier was laid to isolate the old producing zone. According to two Oil India Limited employees aware of the operation, cementing work had been completed on May 26.
Repairing while waiting
Then it was time to wait before the new sand zone could be “perforated” with a blast using explosives. “Before perforating, you have to give it some time,” said an Oil India employee who has been involved in workover operations. “And when your new perforation target is above the existing zone, the time gap is supposed to be even longer.”
However, the waiting time could be used productively – to carry out repair work. “This is already NPT or non-production time, so it is a good time to do minor repair works instead of closing down the well to do repairs during production time,” said the official. “It is standard practice across the oil industry and it is perfectly safe if you wait out a specific time for the cement casing to settle.”
In this case, the team at work was assigned to replace the well head, the pressure-containing component at the surface of the well. However, that would mean taking out the blowout preventer first, and relying on the cement plug entirely – yet again, a fairly safe thing to do if the cement plug is solid.
Gas gushes out
However, on May 27, as the team took off the blowout preventer and started replacing the oil head, gas started gushing out from the well. The cement plug had failed.
According to a person with over 20 years of experience in the company’s chemical department, the standard “cement on waiting” time before a blowout preventer can be removed is 48 hours. “In all likelihood, the cement will set in much less time, but it is best to wait out for 48 hours which they did not seem to have,” said the official.
However, the official cautioned against drawing a direct cause-and-effect relationship between the blowout and the allegedly premature opening of the blowout preventer. “These are not linear events,” he said. “The BOP had to be removed at some point anyway and maybe the blowout would have happened later too. All we can say with surety is that the blowout would have not happened the day it did.”
Independent observers alleged other lapses too. Prodip Kumar Saikia, who was one of the consultants hired by Oil Limited when the well was discovered in 2003, said there should have been another reinforcement plug in addition to the cement casing. “I know a thing or two about this well,” he said. “It’s an extremely high-pressure well and you can’t rely on just the chemical plug [the cement shield]; you need a mechanical plug too.”
Finally, a functionary of the company’s workers’ union blamed privatisation. “We are accused of being too slow because we put safety first,” he said. “This is a textbook case of a private contractor being in a rush to finish the job.”
Tridiv Hazarika, the Oil India spokesperson, declined to address specific allegations. The company had ordered an in-house technical audit, he said. “It could be a machine failure, a process failure, a human error or a combination of the three – let the results of the audit come out,” said Hazarika.
Containment woes
Next, the alleged containment lapses. Once disaster struck, did Oil India do enough?
A retired geologist with 32 years of experience of working at the company said the simple answer was no. The reasons for this, he said, were structural. Oil India Limited, he alleged, had failed to develop the required in-house expertise to deal with blowouts, despite having suffered because of this in the past.
In 2005, after a blowout in one of its oil wells in Dikom in Upper Assam’s Dibrugarh district had taken 45 days and foreign experts to be stabilised, the company set up a unit to deal with such crises. However, both current and former employees alleged the company had invested very little in acquiring cutting-edge equipment and training the unit’s personnel. “If you have a dedicated team of your own and provide them real hands-on exposure in other blowout sites, you will be able to at least provide a strong initial response,” said the retired geologist. “But over the years, people from this unit have been outsourced to other departments such as creative and production.”
The retired geologist said that, while he understood the reluctance of the company to invest huge amounts of money in a “workforce that would remain idle for most of the year”, he did not understand why the company had not signed an annual contract with foreign blowout control companies. “You should at least have an MoU in place that mandates experts to arrive in not more than two days using a chartered airplane instead of blaming the pandemic lockdown,” he said.
A current employee agreed: “Yes, it is our deficiency.”
Flying in the experts
After the blowout was reported on May 27, the first external experts to arrive were a team from the Oil and Natural Gas Corporation’s Nazira unit. They reached the site on May 28, according to Hazarika.
However, three members of ONGC’s crisis management team arrived from Vadodara only on the “third or fourth day”, said Hazarika.
The three–member blowout control experts from Singapore arrived on June 7. “We had started talking to them on the 29th itself,” said Hazarika. “But because of the pandemic situation, it took some time for them to get their visa and flight clearances.”
Hazarika said travel restrictions because of Covid-19 had delayed their arrival by around five days.
The spokesperson denied allegations that Oil India had not cultivated enough in-house expertise. “Even if you have n number of people in your own crisis management team, you will not be able to handle a blowout of this proportion,” he said. “Why? For the simple reason that you can’t simulate a blowout on a computer. To face a blowout, you have to actually face it and learn from it.”
Besides, he said, Oil India Limited had purchased several pieces of modern equipment after the 2005 incident. “One must note that neither the Singapore experts nor ONGG have brought in their own equipment; they are using OIL’s,” he claimed. “Also, there have been n number of blowouts since 2005 and we have been able to control them on our own.”
He added, “There is a reason blowout control companies exist – companies 30 times bigger than us, even in the Middle East, have used their services.”
Machines in the way
There are other allegations that the accident could have been tackled differently. According to Saikia, Oil India Limited’s mitigation strategy was flawed till very recently. They treated it as a solely gas leak, but the blowout had also released a large amount of condensate, or low-density hydrocarbon liquids. These spewed out liquids required different containment measures, he explained.
Yet, Oil India officials overseeing the operation said that all that was possible was being done. “Our first priority was to minimise the damage so we had to clear everything in the area,” said an official part of the on-ground mitigation efforts.
That has been a task as it was an active rig and was full of equipment. Movement in metal machines could cause friction and spark a fire.
“There was a huge crane hardly five to ten metres from the well, which meant we could use no machinery – 20-30 of our people pulled it out with their bare hands,” the official claimed.
There are several ways to plug a blowout. Oil India Limited aims to place a blowout preventer, which weighs around three tonnes, on the well. For that, a “hydraulic lander” that can dodge obstacles is being made in the company’s central workshop in Duliajan.
But there many obstacles. Apart from the cranes and heavy machinery, there stood the drilling mast – a telephone tower-like structure that supports the weight of the drilling pipes and allows them to be lifted in and out of the oil well. “Any contact with the mask would lead to friction which could lead to ignition,” said an official involved in the exercise.
The fire took the mast down on Tuesday. “We will have to admit that it was a big relief,” said the official. But there is still a long way to go. “You can’t control a blowout of this intensity in a couple of days,” he said. “We have to be given the time that it takes.”
The official, for his part, admitted there had been lapses: “I think it is a big learning for us – we have to just dig out the positives and move on.”
Buy an annual Scroll Membership to support independent journalism and get special benefits.
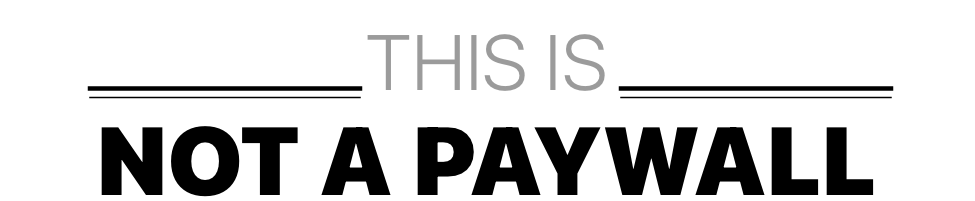
Our journalism is for everyone. But you can get special privileges by buying an annual Scroll Membership. Sign up today!