Design has a complex relationship with origins. The Royal Enfield motorcycle, the Godrej Almirah and the pressure cooker were all ‘foreign’ but were re-drawn as products in India, giving them a new meaning. These products are a marriage of craft and industry and have given India a unique form characterized by appropriating something new and merging it with something old and something borrowed often referred to as ‘jugaad’. Jugaad shows that India is intuitively adept at finding solutions through the oldest of human conditions – ‘scarcity’. In time it became sophisticated as we see in the Nano where Indian design is at its most ingenious and adaptable. This product is a result of multiple constraints of cost, size and mobility. The Nano is small and frugal but has thirty-eight pending patents. Designing with scarcity is not a products-only playground. ‘Frugal’ is a bit of a crude word, but has been adopted globally as an important design currency in an unpredictable world.
IDLI PATHRAM
A utensil to prepare India’s favourite breakfast, idlis
Date of Origin: 1950s
Material: Stainless steel, aluminium
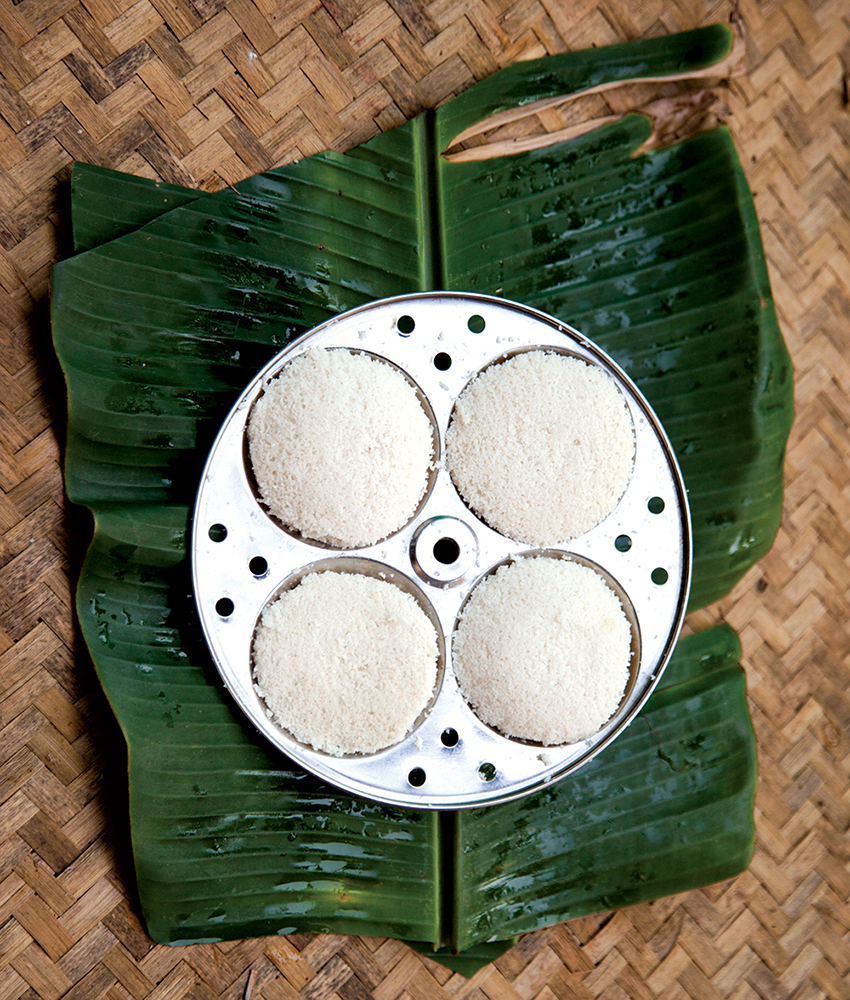
If one were to divide India along a food fault line, it would have to be a North-South one: the north with its chai-samosa and the South with its idli-dosa. And yet, this line is by no means set in stone. It’s the Tamilians who have taken the idli northwards, and beyond Indian shores to America, where it is sold as a diet meal with the perfect mix of carbohydrates and proteins. But it’s the north that gave idli-making a modern twist: smartly pressure-cooking the idlis in a custom-made stainless steel stand called the idli pathram. The utensil consists of two-three trays put together with a steel rod and a screw. The holes in the trays help in steaming the idlis.
Behind the idli-maker lays the story of stainless steel. From the early 1950s, due to huge government subsidies the steel industry flourished and stainless steel started filtering into Indian kitchens, first in Delhi, Bombay and Poona, and then Madras. In the kitchen, stainless steel took over traditional brass, bronze, copper and tin vessels largely due to the former’s affordability and the high maintenance of polishing and cleaning required by traditional metals.
The traditional idli pathram, made of iron, was an important part of any Tamil-Brahmin kitchen. All kitchens were equipped with many different sizes of this utensil. In the big cities like Delhi and Bombay, idlis were eaten only at South Indian specialty restaurants. the growing popularity of these restaurants that offered a cuisine different from the North Indian’s daily palate of wheat, rice and vegetables meant that the idli-maker found its way into traditional North Indian kitchens and Sunday afternoon lunches. Due to easy access to stainless steel in the 1970s, steel idli pathrams started being sold in the markets. The convenience of being able to make idlis almost instantly in an idli-maker is what helped the tradition of the idli disperse itself far and wide.
SINTEX TANK
Water storage tank for all of India
Date of Origin: 1979
Material: Virgin and food grade polythylene plastic
Rain is a real challenge in some parts of India. Fatehpur Sikri was abandoned in the twelfth century because of drought. in the West rain comes rarely but in the East it comes in floods. Only forty-five per cent of urban homes and one-fourth of rural homes have access to tap water. So storage of water and its transportation to deficient areas makes overhead water storage tanks essential. This is why the strong, lightweight, portable, easy-to-maintain, Sintex water tank has found many takers. They might be black and bulky but nevertheless India has formed a relationship with them as water is what maintains the city’s chain of life.
Sintex tanks are truly innovative borrowing plastic technology not from the water industry but from a completely disconnected textile industry. Sintex was originally a textile company with a small plastics unit acquired in the early 1970s when the textile business needed card cans (used for cleaning fibre), for which the company had imported plastic rotational moulding technology. This idea of plastics in the textile industry did not work out. But the company did not stop there, thinking laterally to see if the rusty overhead water tanks could be replaced with new plastic ones that the company could build. This is where the name of the triple-layer water tanks came from – ‘Sin’ from the sintering process of fusing plastics together and ‘tex’ from textiles, which is what the plastic technology was initially for. The company’s ‘one-piece-ready plastic tank’ was exhibited for the first time at the ChemTech exhibition in Bombay in 1975. Around that time there was a cement and steel crunch in the country, and as overhead tanks polluted the water it led to the debut in 1979 of Sintex water tanks, made from virgin and food grade polyethylene.
They were lightweight, durable and foolproof, and the black colour was chosen to block the sun’s harmful UV rays. Consulting architects shunned the idea as the tanks looked ugly on top of buildings; nevertheless, it was the functionality of clean, safe and leak-proof material that won people over. Though now Sintex water tanks are available in white too.
CH-4 CHAIR
India’s first modernist workspace chair with steel tubing.
Date of Origin: 1958, Bombay
Material: Steel, wood and cane
The CH-4 chair was a groundbreaking piece of innovation, not only in its cantilevered one-piece frame, when most chairs usually had four legs, but also in its use of steel that ushered in a completely new material for the construction of chairs. This chair is what transformed India’s old offices into modern spaces, which had been using only heavy wooden furniture. At the turn of the twentieth century, Godrej, the company that had successfully established a niche in the furniture industry with steel almirahs and patented foolproof safes, started modernizing India’s officescape by replacing wooden furniture with steel. By the early 1950s, Godrej had successfully introduced a gamut of new designs for tables, office partitions, shelves, cupboards, and of course the iconic CH-4 chair.
This transformation had its roots in Prime Minister Jawaharlal Nehru’s vision of Modern India, which resulted in the 1951 collaboration with Le Corbusier to design Chandigarh, the first planned city of India. Nehru made Chandigarh the national symbol of freedom and modernity. To express freedom in every aspect of life, Indian Modernism was further developed in the use of modernist architecture for the construction of homes, cars and even steel factories. Seizing the opportunity, Godrej adopted Nehru’s vision and commissioned India’s first modernist workspace – the offices of Madhya Pradesh State Electricity Board. Amongst the chairs, tables and partitions, the CH-4 chair alone became iconic. In design and function, the CH-4 epitomized the ‘less is more’ aesthetic and sold millions of units.
Made from electricity-resistant welded steel tubing, the CH-4 is cantilever in shape with a teak and plastic cane seat and back rest. It was initially available in olive green with black wood elements and was lightweight and elegant in design. Launched in 1958, it did not make headlines but was placed in every office in the country. Further additions to the design included arm rests and office tables also in bent tubular steel.
Its inspiration was the Bauhaus designer Marcel Breuer’s 1925 Wassily chair, which first used bent tubular steel and canvas, as well as his 1928 Thonet chair fashioned from tubular metal and wood – the novel cantilevered principle of support requiring two rather than the traditional four legs for support. The CH-4 chair was similar but indigenously produced; the first models were with teak trimmings along the arms and the backrest. While the difference in its design was minimal, it revolutionized the office furniture industry, moving it away from the use of natural materials to the use of mass-produced industrial materials, minimalist styling and advanced manufacturing techniques. Steel meant evolution, steel was modern and it was essential to the industrialization of India.
Furniture design has since then moved from modernist to post-modernist, using wire, corian and fibreglass. Godrej, too, has expanded its furniture collection, but the CH-4 chair continues to be produced and remains popular because its design has undergone much ergonomic evolution, like following the curve of the back or introducing the swivel.
BANTA
A banta or marble plugs this bottle that opens with a pop.
Date of Origin: 1870s, Delhi
Material: Glass, marble, water, lemon juice, sugar, black salt, cumin
Goli soda or banta is lemonade that pops when opened, and goli is the marble stuck in the bottle to hold the fizz. This corkless bottle, called the Codd-neck bottle (after its creator Hiram Codd), is a late-nineteenth century design made in the UK, but it is India that gave the drink hundreds of flavours and an indelible connection to youth, playfulness, taste and patriotism. Goli soda or banta is also how a whole generation in India remembers their childhood, and banta is considered the drink of the nation because the pop, the place and the taste are considered definitively Indian.
The most common kind of banta is made with lemon juice, ice and sugar, a pinch of black salt and cumin seeds, thus giving an international lemon soda an Indian flavour through the addition of spices. Though this is the mother recipe that unites the entire country, it is called banta in the north and goli in the south, and there are many regional and local variations too. For example in Mangalore, there are several versions with different names: ‘nannari’ if it is made with ginger, ‘impto’ when it has more of a cola flavour, ‘chappe’ if it is without spice, and simply ‘colour soda’ if it has red, blue or yellow colour added to it.
Excerpted with permission from Pukka Indian: 100 Objects that Define India, Jahnvi Lakhota Nandan, Roli Books.
Buy an annual Scroll Membership to support independent journalism and get special benefits.
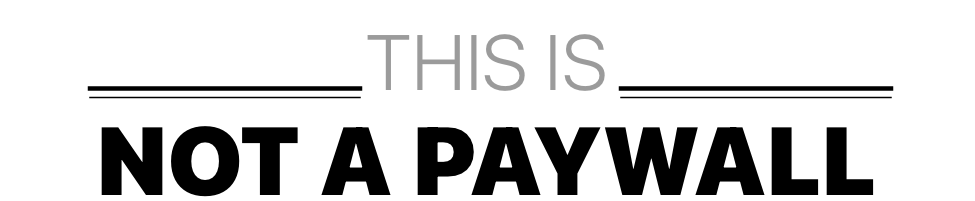
Our journalism is for everyone. But you can get special privileges by buying an annual Scroll Membership. Sign up today!