Can nature prove to be the best furniture designer? Early prototypes of chairs growing from a field in Derbyshire in the British countryside is showing exciting possibilities.
“We’ve taken a complete rethink of how wood is used as a material,” said designer Gavin Munro. His production method upends traditional furniture manufacturing processes that involve cutting down trees, trucking logs, sawing the wood, then gluing back them together, generating a lot of industrial and ecological waste in the process.
Over the last four years, Munro and his team at Full Grown have been nurturing hundreds of willow trees, patiently waiting for the right harvest time. Guided by Munro’s studies in tree shaping and botanical craftsmanship, the trained furniture designer is using grafting techniques to coax the tree branches to form chairs, tables and lamp, and frames.
Coax is key word here. “The first breakthrough was realising that you can’t force the trees – a tortured branch just dies and other pops up elsewhere,” Munro explained on his website.
When nature supplies both material and creative force, the product designer’s job to nurture, observe, and adapt – as opposed to the usual draw, spec, and replicate. Designers can even forge a unique attachment with the objects they shape inch-by-inch over the span of a few years.
“To say that we get attached could be an understatement! It’s very oddly emotive having a herd of chairs and lamps to look after,” Munro tells Quartz. “We have had some favorites from the beginning that have shone every season and others that have lost a branch mid way to our great despair. There’s also a few that were abandoned to be experiments that have returned to form and surprised us all.”
A customer may need to wait longer for a custom chair, but in the age of instant 3D-printed objects, high speed manufacturing and overnight deliveries, Munro offers a model of “mass manufacturing meets delayed gratification”. The reward is a unique and lasting object, sturdier than most manufactured furniture because it has no seams.
The idea began germinating in Munro’s youth – observing an overgrown bonsai tree take the shape of the chair on its own, and later experimenting with driftwood during his years living in San Francisco, California after college. But a series of operations to straighten his spine that kept him in a brace for weeks as a child, gave Munro an indelible first-hand experience of being grafted. “It’s where I learnt patience,” he said.
There have been earlier advocates of “grown furniture,” like the British designer Christopher Cattle, who has been using the technique since the late 1970s. In the early 1900s, American banker John Krubsack grew an elaborate high back chair from box elder saplings – a project that took 11 years.
Customers will not have to wait that long for Munro’s furniture, about 3-4 years for willow chairs and 6-10 years for oak. “For those of you who like wine or whiskey, I’m sure you’ll appreciate, a bit of maturing is not a bad thing,” he said.
But like the patient gardener, Munro is cautious about expanding his enterprise too quickly. “This is an art form that’s only just found its feet.” he says. “We have a few cycles of harvest under our belt before making any firm decisions about that. There is plenty of potential for large scalability but this is an idea that progresses in terms of years and decades.”
This article was originally published on qz.com.
(Full Grown Ltd.)
(Full Grown Ltd.)
“We’ve taken a complete rethink of how wood is used as a material,” said designer Gavin Munro. His production method upends traditional furniture manufacturing processes that involve cutting down trees, trucking logs, sawing the wood, then gluing back them together, generating a lot of industrial and ecological waste in the process.
Over the last four years, Munro and his team at Full Grown have been nurturing hundreds of willow trees, patiently waiting for the right harvest time. Guided by Munro’s studies in tree shaping and botanical craftsmanship, the trained furniture designer is using grafting techniques to coax the tree branches to form chairs, tables and lamp, and frames.
Coax is key word here. “The first breakthrough was realising that you can’t force the trees – a tortured branch just dies and other pops up elsewhere,” Munro explained on his website.
When nature supplies both material and creative force, the product designer’s job to nurture, observe, and adapt – as opposed to the usual draw, spec, and replicate. Designers can even forge a unique attachment with the objects they shape inch-by-inch over the span of a few years.
“To say that we get attached could be an understatement! It’s very oddly emotive having a herd of chairs and lamps to look after,” Munro tells Quartz. “We have had some favorites from the beginning that have shone every season and others that have lost a branch mid way to our great despair. There’s also a few that were abandoned to be experiments that have returned to form and surprised us all.”
How to grow a chair in four steps(Full Grown Ltd)
A customer may need to wait longer for a custom chair, but in the age of instant 3D-printed objects, high speed manufacturing and overnight deliveries, Munro offers a model of “mass manufacturing meets delayed gratification”. The reward is a unique and lasting object, sturdier than most manufactured furniture because it has no seams.
Munro with a metal halo brace after a series of spinal cord operations.(Gavin Munro)
The idea began germinating in Munro’s youth – observing an overgrown bonsai tree take the shape of the chair on its own, and later experimenting with driftwood during his years living in San Francisco, California after college. But a series of operations to straighten his spine that kept him in a brace for weeks as a child, gave Munro an indelible first-hand experience of being grafted. “It’s where I learnt patience,” he said.
There have been earlier advocates of “grown furniture,” like the British designer Christopher Cattle, who has been using the technique since the late 1970s. In the early 1900s, American banker John Krubsack grew an elaborate high back chair from box elder saplings – a project that took 11 years.
Furniture Field in Derbyshire, UK(Fully Grown Ltd.)
Customers will not have to wait that long for Munro’s furniture, about 3-4 years for willow chairs and 6-10 years for oak. “For those of you who like wine or whiskey, I’m sure you’ll appreciate, a bit of maturing is not a bad thing,” he said.
But like the patient gardener, Munro is cautious about expanding his enterprise too quickly. “This is an art form that’s only just found its feet.” he says. “We have a few cycles of harvest under our belt before making any firm decisions about that. There is plenty of potential for large scalability but this is an idea that progresses in terms of years and decades.”
This article was originally published on qz.com.
Scroll has produced award-winning journalism despite violent threats, falling ad revenues and rising costs. Support our work. Become a member today.
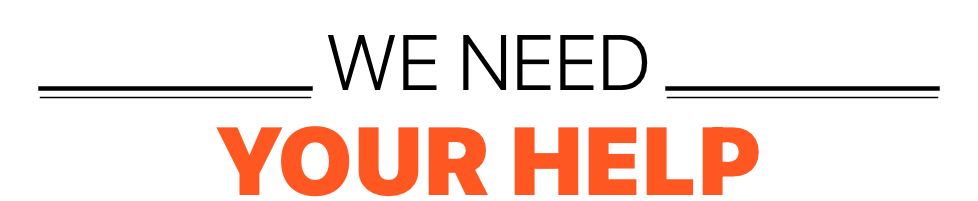
In these volatile times, Scroll remains steadfastly courageous, nuanced and comprehensive. Become a Scroll Member and support our award-winning reportage, commentary and culture writing.