Starting in October, Punjab and Haryana garner a lot of attention during the paddy harvesting season every year. The short window between the harvesting of paddy and sowing of wheat, besides the high cost of straw management, forces farmers to reach for the matchstick instead. This year, the window shrank further due to late rains that delayed paddy harvesting.
The burning is often blamed for the severe air pollution in Delhi in these months. The share of farm fires to the capital’s pollution, however, depends on daily instances of fires and the weather conditions like wind speed and direction.
This year, the contribution of farm fires to PM 2.5 in Delhi’s air varied from 6% to 48% between November 1 and November 15, showed data from the System of Air Quality and Weather Forecasting And Research of the Pune-based Indian Institute of Tropical Meteorology. The number of farm fires in the region, however, reached the peak of 5,430 on November 8, which was higher than last year’s peak of around 4,500.
Last month, the Supreme Court rebuked the Union government for blaming farmers and not providing them machines to manage the surplus paddy straw. Besides the on-farm management, the options of using the paddy straw to produce energy at biomass power plants and biogas units, compressing it into fuel pellets and briquettes have also been tried on various scales.
Biomass availability
India has traditionally relied on biomass for its energy needs. Wood, bushes, straws and cow dung are regularly fed in household earthen stoves and small furnaces. Biomass power plants do the same process in a controlled environment to run steam turbines that produce electricity.
The biomass power sector generates local employment because of its labour intensity but the sector is battling challenges like high running costs, feed procurement and competition from solar and wind which are comparatively cheaper to produce.
“Biomass has a good scope considering India has a target of net-zero emissions by 2070,” Manjushree Banerjee, an independent consultant on energy access, told Mongabay-India. “Currently, most of biomass energy production is captive which means industries are using biomass to run their own units to save on electricity bills especially in states where the industrial tariff is very high.”
“Sugar mills are the first movers in this space as they already have bagasse as a byproduct of sugar-making process, which can be reused as a raw material for producing power,” Banerjee said.
According to the October data of the central government, biomass-based power had a share of over 10% (10.1 gigawatts) in the 103 GW of total installed capacity of renewable power in India. While wind and solar power account for over 85% of the total installed capacity of renewable power in the country.
In fact, Punjab has the highest power potential from biomass in the country at 3,172 megawatts especially with the generation of 2 crore tonnes of paddy straw. But the installed capacity is low.
“We have 11 biomass power plants in the state with a total capacity of 97.50 megawatts,” RK Gupta, joint director (biomass) at Punjab Energy Development Agency, told Mongabay-India. “These consume 8,80,000 metric tonnes of paddy straw every year. Two more power plants of four megawatts and 10 megawatts capacities are planned.”
But biomass power plants are not easy to run as they have to deal with issues of procurement of feed, storage and day-to-day running costs.
“Primary challenge for biomass power generation is feed and the land required to grow and store this feed,” Banerjee said. “Its cost depends on the local situation, distance from which procurement is happening and there is no formal regulation on this aspect. The everyday management is thus challenging.”
Paddy straw-based plant has more challenges as the raw material is high in silica, has low bulk density, high ash content and alkaline metals which result in incomplete combustion and adverse impact on the equipment.
The 18 megawatts biomass plant of Sukhbir Agro Energy Limited near Ferozepur, Punjab, consumes around 2,00,000 tonnes of paddy straw every year. “Unlike a solar energy park, which is a one-time investment, we have to deal with day-to-day issues like procurement and storage,” complained Arvind Bedi, general manager of the plant. “Though we are able to overcome technological gaps, there are other challenges like we cannot use straw with high moisture because as that damages the machinery.”
In August, the cabinet of the Punjab government approved cumulative fiscal incentives of Rs 25 crores to the first 50 industries that install paddy straw-based boilers. The cabinet also decided to make panchayat land available to industries for storage of paddy straw with a lease agreement up to 33 years besides making balers available on priority in areas where the straw is used as fuel in boilers.
Besides biomass power plants, Punjab has also given approval to a compressed biogas plant while a bio-CNG plant will start operations early next year, both of which will use paddy straw.
A one-megawatt biogas power plant is already operational in the Fazilka district of the state. It is feeding energy into the grid.
“Biogas is the cleanest way to deal with paddy straw because not only there is no combustion involved, you also get the slurry which is rich in micronutrients and can be used as a bio-fertiliser,” Ram Chandra, assistant professor at the Centre for Rural Development and Technology, Indian Institute of Technology, Delhi, who worked to increase the efficiency of the Fazilka plant, told Mongabay-India. “In all other power generation methods, there will be emissions from boilers, creation of ash, and the nutrients of the straw, which should have gone back to the soil, are lost.”
Struggle for tariff
Tough competition from other renewable sources like solar and wind is also proving to be a bane for biomass-based power producers.
“Focus is more towards solar as its generation cost is coming down because of the reducing cost of photovoltaic technology and batteries but in case of biomass the cost is going higher,” Banerjee emphasised.
In Punjab too, the tussle on tariff is on. “Tariffs of solar has gone down to Rs 2.25- Rs 2.50 per unit but for biomass, it is around Rs 8. Most of the power distribution companies and state utilities are reluctant to buy at such a high rate but we need biomass power plants because they help with air pollution,” said Gupta. “The Punjab State Power Corporation Limited is ready to buy at the rate of Rs 4 (per unit) but the developers’ cost is Rs 8 (per unit). To fill this gap, we are requesting the Centre to provide us Rs 5 per unit as viability gap funding. Unless the gap is filled, no developer will come forward to set up more such plants.”
Though the existing biomass power plants are governed by older power purchase agreements which offer varied rates going up to Rs 8.36 per unit, the state government is now mulling reducing the rates by one rupee per unit.
Rising debt
It is not just the high cost of generation and competition that is a matter of concern. There are other issues too. Baler and rake machine combination is used to gather and compress straw into bundles or bales for easy transportation.
Currently, around 500 such machines are operational in Punjab. While those owning and operating these machines earn by selling the straw bales to the biomass plants, farmers get nothing and might even have to pay Rs 500 per acre for getting their fields cleared. This operation can take two days- three days and sometimes farmers are not ready to wait that long and instead they burn the straw.
“There is not much profit margin in this business,” Harbhajan Singh, who supplies bundled straw to the captive biomass power unit of a textile company, told Mongabay-India. “There is an investment in machines, fuel, transportation and labour and hence we cannot pay the farmer and have to charge them if the distance between the field and power plant is more.”
“We used to earn Rs 135-Rs 150 per quintal of straw till last year and the payment would also get delayed,” he said. “This year, we made a union of baler owners and fixed the selling price at Rs 174. Also, we decided not to charge the farmers because paddy harvesting was delayed and they are not willing to waste more time in bailing.”
Plant managers feel the government should incentivise the farmers and also extend the subsidy to big machines. “We face a shortage of straw if farmers indulge in burning,” said Arvind Bedi. “If those who go for bailing get financial support, the fire incidents will reduce.”
He stressed that the state should “also subsidise big baler machines which can clear around 100-acre in a day because the window between paddy harvesting and sowing of wheat is small”.
But the uncertainty in this sector has also burnt the fingers of many farmers. The 12-megawatts biomass-based power plant established by the Punjab Biomass Power Limited near Patiala closed down in 2017 after running into losses, leaving several farmers supplying the raw material in the lurch.
“They motivated us to buy the high-cost machines but the company started defaulting on payments after a few years,” shared Sukhchain Singh of Magar village, Patiala district. “We took loans to invest in machines and spent money on the collection and transportation of straw. The baler machine was worth Rs 9 lakh- Rs 10 lakh at that time … we two brothers have two machines and now have bills of Rs 20 lakh pending in payments from the company.”
“We could not repay the loan and had to sell one acre of land,” said Sukhchain Singh. “We can say that the biomass plant gobbled up one acre of our land. The company is yet to pay Rs 4 crore of around 50 farmers of the area.”
“When the plant was operational, it helped reduce farm fires in the area by 75% and also generated employment for locals,” Sukhchain Singh said. “But now farmers have gone back to burning the straw.”
Mongabay India tried to speak to company officials but could not reach them despite repeated attempts at their official contact number.
Pellets and briquettes
In addition to other measures, certain experiments are going on to compress straw into briquettes and pellets, which increases the bulk density and calorific value of the straw for use as an alternative to fossil fuel in industries.
“We are able to make briquettes which can be used to fire industrial boilers and brick kilns,” shared Jatinder Kaur Arora, executive director of Punjab State Council for Science and Technology. “The processing of paddy straw is a huge challenge as it causes immense wear and tear in machinery. We were able to overcome that through technological innovations.”
“These briquettes could replace fossil fuel in conventional brick kilns and now trials are on to establish combustion behaviour in industrial boilers,” Kaur Arora said.
However, only big companies which have specifically set up biomass-based boilers are currently able to use paddy straw briquettes. Existing boilers need modifications to be able to use paddy straw.
Also, pellets made from paddy straw can be another source of alternative fuel for industries.
“We usually serve pharmaceutical, food processing and dyeing industries which are using these pellets to generate steam and run turbines,” revealed Sukhmeet Singh, who is the chief executive officer of A2P Energy Solutions Private Limited.
“In current times, responsible brands looking for green alternatives are opting for our fuel but we need capital investment to scale up and this cannot be typical venture capital where short-term benefits are seen,” Sukhmeet Singh said. “We are focussing on investors who are here for the long term and are focussing on sustainability rather than only returns.”
This article first appeared on Mongabay.
Scroll has produced award-winning journalism despite violent threats, falling ad revenues and rising costs. Support our work. Become a member today.
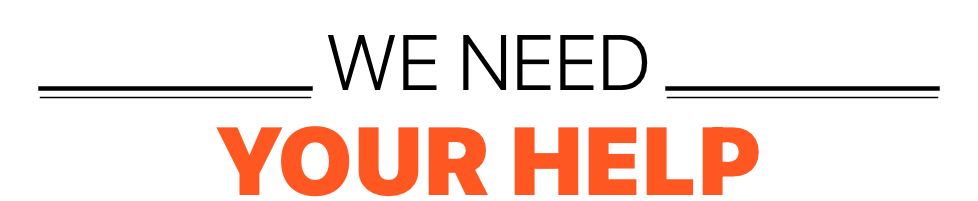
In these volatile times, Scroll remains steadfastly courageous, nuanced and comprehensive. Become a Scroll Member and support our award-winning reportage, commentary and culture writing.